RM Surveys integrate the Leica RTC360 3D laser scanner for the redevelopment of a Perth shopping centre
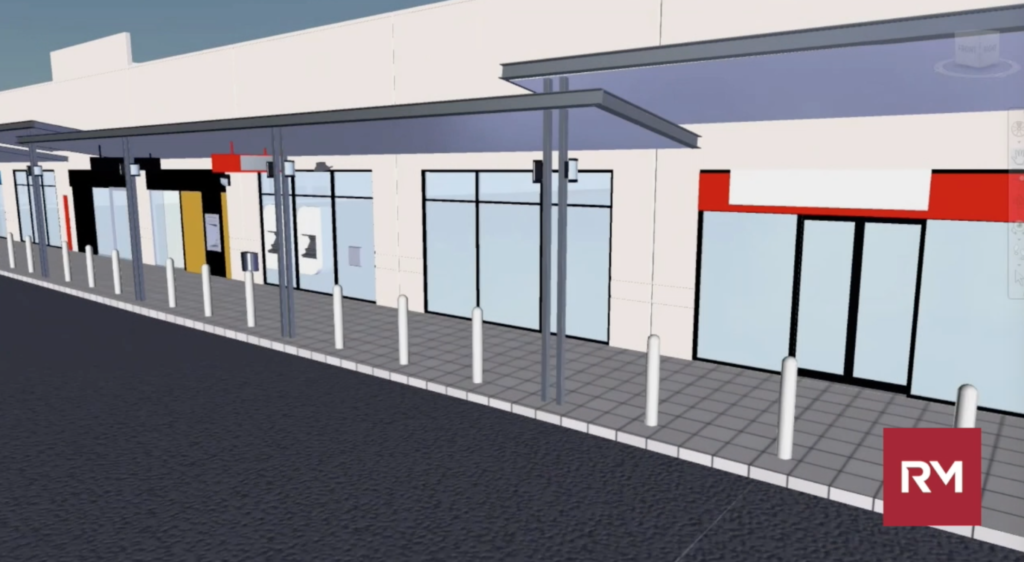
Introduction
RM Surveys integrate the Leica RTC360 3D laser scanner for the redevelopment of a Perth shopping centre
RM Surveys, an Australian firm who provide end to end survey solutions for commercial, resource and residential industries was excited to participate in its recent project when it was contacted by an architect firm about creating a survey-grade architectural and structural Revit BIM model for the redevelopment of the Kardinya Park Shopping Centre. After all, the firm had a new Leica RTC360 3D laser scanner.
The Perth shopping centre is expanding and upgrading the facilities to elevate the overall appeal of the centre and to bring new shops, mixed-use amenities and a multi-deck covered parking to the local community. The client needed a Revit BIM model for architects, engineers and facility managers to accurately plan the work needed. The RM Surveys team was tasked by the architect firm to capture the 90,000m2 site area, supply a complete as-built deliverable of BIM Level of Development (LOD) 300 for the exterior and LOD 200 for interior for general planning, early involvement and consultation review and to help with the conceptual design.
Scanning and modelling with speed.
The RM Surveys team used a couple of Leica Geosystems solutions to capture, model and analyse the data. Externally there were very drastic topographic changes along the southwestern corner of the site with high retaining walls. To better capture and represent the complex topography in a 3D space the RM Surveys team used a couple of Leica Geosystems solutions to capture, model and analyse the data.
Starting with the Leica ScanStation P40 survey-grade laser scanner, the surveyors used the P40 for the external facades due to its long-range capability.
It was the first project the team had an opportunity to integrate its new RTC360 3D laser scanner into its workflow.
Why the RTC360? The RTC360 was chosen for its portability, in-field pre-registration of captured data and strong visualising capabilities. During the day the team worked at a live shopping centre site, and with shoppers strolling around, the compact and sleek design of the RTC360 did not obstruct shoppers. Typically, when scanning, high-traffic areas such as shopping centres pedestrians create ‘ghost points’ which overlay the object of interest and need to be manually removed during the post-processing phase in the office. After the removal of these ghost points, they leave gaps of the missing points and are visible in the background of the final scan data. Utilising the Double Scan feature of the RTC360 meant that the data captured resulted in clean and complete point clouds and boosted productivity for the team.
Another advantage of integrating the RTC360 comes down to the compact design of the 3D laser scanner combined with the Scan & Go UPLIFT 500 as a ready solution to capture ceiling cavities.
The high-speed of the RTC360 was apparent to RM Surveys team when it comes to improving site workflow – the team doubled the number of scans they were able to do per day. The automated targetless field registration (based on VIS technology) and the seamless, automated transfer of data from site to office reduced the time spent in the field and the time the team had to spend on tightening the final registration, helping them eliminate a large portion of office work. To quantify the time saving, the team was able to complete the job 45% faster using the RTC360.
The team conducted approximately 150 scans per day using the RTC360 with most scans completed in medium resolution, and some of the smaller areas of the shopping centre in low resolution.
A total of 1,200 interior and exterior scans resulted from the project. Initially, the team was tasked to complete the external work. After seeing the data, the client was so impressed with the deliverable that the team was also hired and able to complete the internal scans within five days.
The captured data from these scans were cleaned and finally registered using Leica Cyclone REGISTER post-processing office software. Autodesk ReCap was used to produce rcp files for the LOD 200 and for more detail LOD 300 modelling in Autodesk Revit.
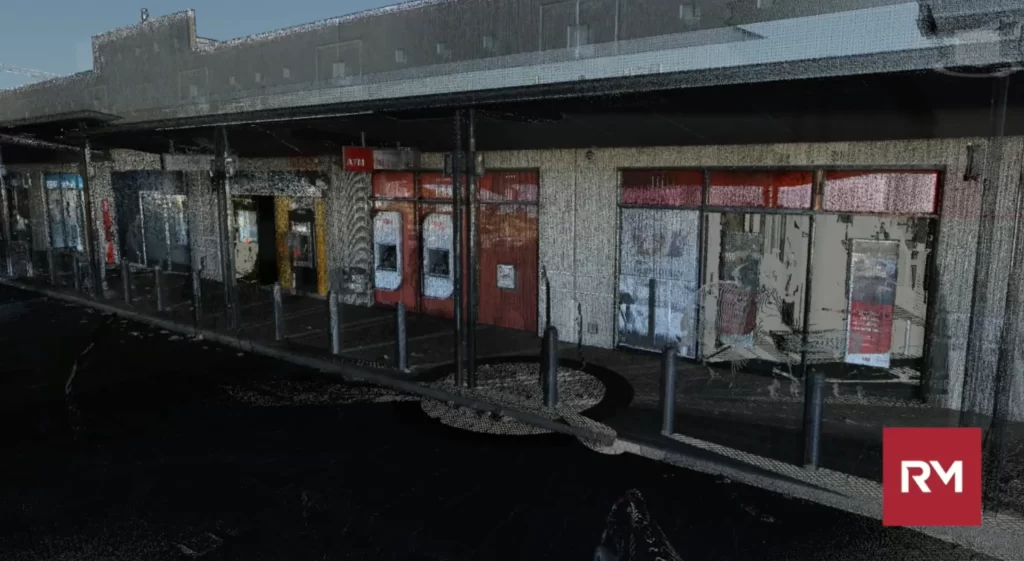
Strategy & Consulting
Lessons learned
From the get-go, the team approached the project hoping that they would do the full scope and planned all the surveying methodology according to the full scope. This involved setting up a broad control network and involved drone capture, ground-penetrating radar and consultation with licensed surveyors.
In addition, the RM Survey team ensured that they were consulted as spatial consultants, as to what data would be used for moving forward.
It’s important to note the consultation and communication early in the project scope. For the RM Surveys team this involved consulting on the accuracy of drone data compared to point cloud data captured from the ScanStation P40 and the RTC360.
By consulting and understanding this information early in the project, the team had the foresight for when three months down the track they would be asked by a fabricator if the Revit BIM model was suitable to use to fabricate steel from.
One piece of advice from the RM Survey team is to spend more time in the planning stage, considering multidisciplinary opportunities and foresee what the client’s future requests or questions might be.
By doing an external full site laser scan survey upfront, we were able to save the client time and money by producing information and drawings for multiple sub-contractors without the need for anyone to remobilise to site.
This would not have been possible without the speed and data-rich product achieved by combining the technology of the RTC360, P40 and Leica Cyclone REGISTER. Without this technology, a large amount of this survey would have been completed using traditional methods which takes more time and delivers less information to the client.
This project is just one of many examples where RM Surveys use the latest technology to capture reality and transform it into a 3D model.
Bjorn (Bernie) Bernhardt, RM Surveys Survey Manager – Construction & HDS.
About the author.
Bjorn is a leader in laser scanning and BIM technology with a wealth of experience in infrastructure and commercial construction projects, such as New Perth Stadium. He is a keynote speaker for industry and universities championing spatial technology survey solutions.